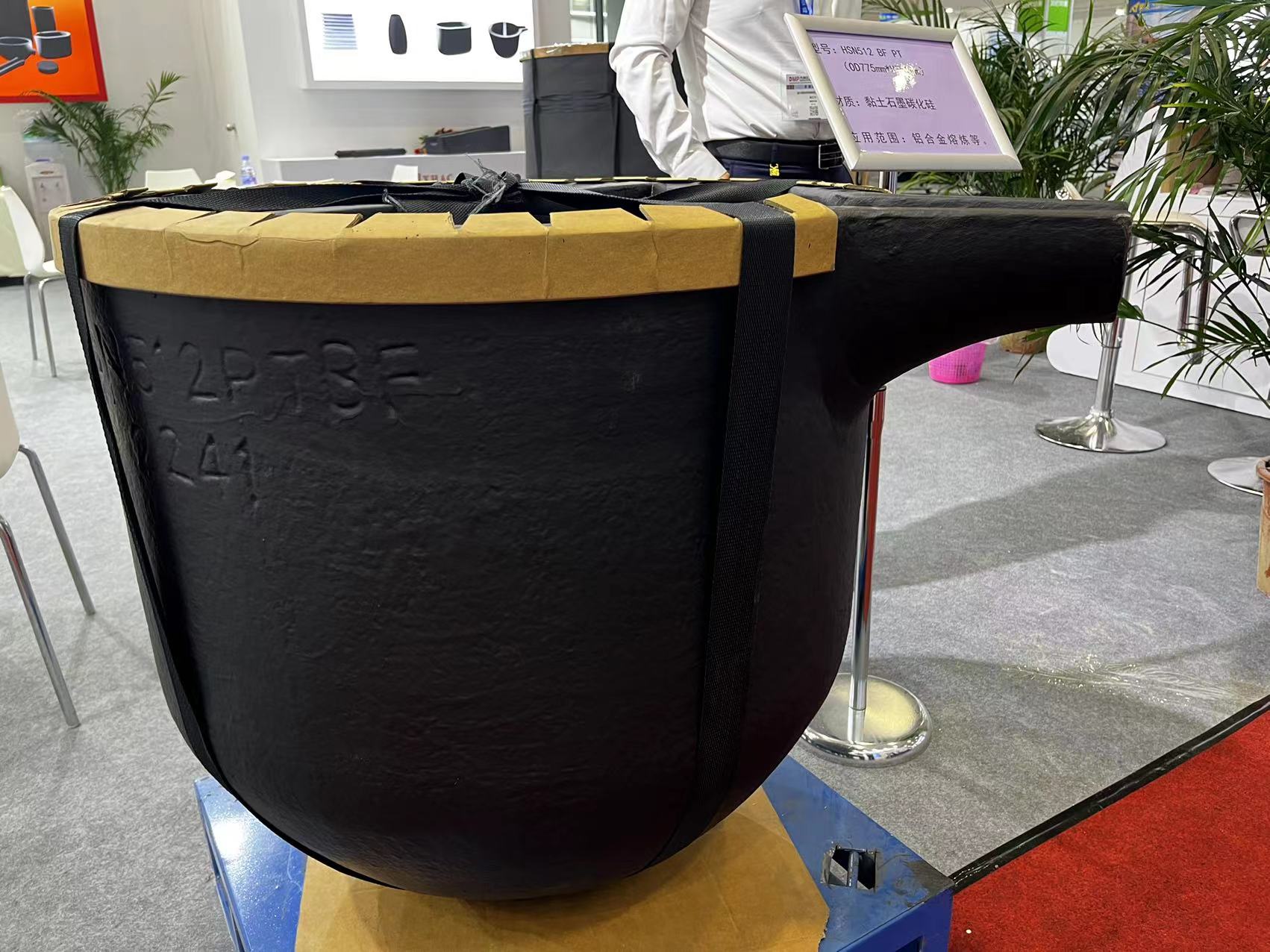
Методот на подготовка на голема јачинаграфит силиконски карбид садЗа топење на метал ги вклучува следниве чекори: 1) подготовка на суровини; 2) примарно мешање; 3) сушење на материјалот; 4) дробење и скрининг; 5) секундарна подготовка на материјал; 6) секундарно мешање; 7) притискање и обликување; 8) сечење и кастрење; 9) сушење; 10) застаклување; 11) примарно отпуштање; 12) импрегнација; 13) секундарно отпуштање; 14) облога; 15) готов производ. Crucible произведен со употреба на оваа нова формула и процес на производство има силна отпорност на висока температура и отпорност на корозија. Просечниот животен век на садот достигнува 7-8 месеци, со униформа и внатрешна структура без дефекти, голема јачина, тенки wallsидови и добра топлинска спроводливост. Покрај тоа, слојот на глазурата и облогата на површината, заедно со повеќе процеси на сушење и отпуштање, значително ја подобруваат отпорноста на корозијата на производот и ја намалуваат потрошувачката на енергија за приближно 30%, со висок степен на витрификација.
Овој метод го вклучува полето на не-ферозно леење на металургија, особено методот на подготовка на графит-силиконски силиконски карбид, за топење на метали.
[Background Technology] Special graphite silicon carbide crucibles are mainly used in non-ferrous metal casting and forging processes, as well as in the recovery and refining of precious metals, and the production of high-temperature and corrosion-resistant products required for plastics, ceramics, glass, cement, rubber, and pharmaceutical manufacturing, as well as corrosion-resistant containers required in the petrochemical industry.
Постојни специјални графитни силиконски карбидни садови за садови и процеси на производство произведуваат производи со просечен животен век од 55 дена, што е премногу кратко. Трошоците за употреба и производство продолжуваат да се зголемуваат, а количината на генериран отпад е исто така голема. Затоа, истражувањето на нов вид специјален графит силиконски карбид и неговиот процес на производство е итен проблем за решавање, бидејќи овие крстовишта имаат значителни апликации во различни индустриски хемиски полиња.
[0004] За решавање на горенаведените проблеми, обезбеден е метод за подготовка на графитни силиконски карбидни крпи за топење на метали. Производите подготвени според овој метод се отпорни на високи температури и корозија, имаат долг животен век и постигнуваат заштеда на енергија, намалување на емисиите, заштита на животната средина и висока стапка на рециклирање на отпад за време на производството, максимизирајќи ја циркулацијата и користењето на ресурсите.
Методот на подготовка на графитни силиконски карбидни крстосници за топење на метал ги вклучува следниве чекори:
- Подготовка на суровини: Силиконските карбид, графит, глина и металик силикон се ставаат во соодветните состојки Хоперс од страна на кран, а програмата PLC автоматски го контролира празнењето и мерење на секој материјал според потребниот сооднос. Пневматските вентили го контролираат празнењето, а најмалку два сензори за мерење се поставени на дното на секој бункер за состојки. По тежината, материјалите се ставаат во машина за мешање со автоматска количка за движење. Првичното додавање на силиконски карбид е 50% од вкупната сума.
- Секундарно мешање: Откако суровините се мешаат во машината за мешање, тие се испуштаат во тампон -бункер, а материјалите во тампон -бункерот се креваат до бункерот за мешање со лифтот за корпи за секундарно мешање. Уредот за отстранување на железо е поставен на портата за празнење на лифтот за корпи, а надлежниот уред за додавање вода е поставен над бункерот за мешање за да додадете вода додека мешате. Стапката на додавање вода е 10L/мин.
- Сушење на материјалот: Влажниот материјал по мешањето се суши во опрема за сушење на температура од 120-150 ° C за да се отстрани влагата. По целосно сушење, материјалот е изваден за природно ладење.
- Скокање и скрининг: Сушениот збиен материјал влегува во опрема за дробење и скрининг за пред-кршење, а потоа влегува во контра напади за понатамошно кршење и истовремено поминува низ опрема за скрининг со 60-мрежа. Честичките поголеми од 0,25мм се враќаат за рециклирање за понатамошно пред-кршење, дробење и скрининг, додека честичките помали од 0,25 мм се испраќаат во бункер.
- Секундарна подготовка на материјал: Материјалите во бункерот за празнење се транспортираат назад во машината за серии за секундарна подготовка. Останатите 50% од силиконскиот карбид се додаваат за време на секундарната подготовка. Материјалите по секундарната подготовка се испраќаат до машината за мешање за повторно мешање.
- Секундарно мешање: За време на секундарниот процес на мешање, се додава специјално решение со вискозност на бункерот за мешање преку специјално решение за додавање на уред со специфична тежина. Специјалното решение се мери со корпа за мерење и се додава во бункерот за мешање.
- Притискање и обликување: Материјалите по секундарното мешање се испраќаат до изостатска бункер за машина за притискање. По вчитувањето, набивањето, празнењето и чистењето во калапот, материјалите се притискаат во изостатската машина за притискање.
- Сечење и кастрење: Ова вклучува сечење на висината и намалување на грабежните ламби. Сечењето се врши со машина за сечење за да се намали садот до потребната висина, а закопките по сечење се исечени.
- Сушење: садот, откако ќе се сече и исече во чекор (8), се испраќа во рерна за сушење за сушење, со температура на сушење од 120-150 ° C. По сушењето, се чува топло за 1-2 часа. Рерната за сушење е опремена со систем за прилагодување на воздушниот канал, кој се состои од неколку прилагодливи алуминиумски плочи. Овие прилагодливи алуминиумски плочи се распоредени на двете внатрешни страни на рерната за сушење, со воздушен канал помеѓу секои две алуминиумски плочи. Јазот помеѓу секои две алуминиумски плочи се прилагодува за регулирање на воздушниот канал.
- Заглавување: Глазурата се прави со мешање на глазура материјали со вода, вклучувајќи бентонит, огноотпорна глина, стаклен прав, прашок од фелдспар и натриум карбоксиметил целулоза. Глазурата се нанесува рачно со четка за време на застаклување.
- Примарно отпуштање: Крвките со применета глазура се отпуштаат еднаш во печка 28-30 часа. За подобрување на ефикасноста на отпуштање, на дното на печката е поставен кревет за печка со лавиринт со ефект на запечатување и блокада на воздухот. Креветот за печка има долен слој на запечатување памук, а над памукот за запечатување, има слој на изолација од тули, формирајќи кревет за печка од лавиринт.
- Импрегнација: Отпуштениот сад е ставен во резервоарот за импрегнација за вакуум и импрегнација на притисок. Решението за импрегнација се транспортира во резервоарот за импрегнација преку запечатен гасовод, а времето на импрегнација е 45-60 минути.
- Секундарно отпуштање: Импрегнираниот сад е ставен во печка за секундарно отпуштање 2 часа.
- Облога: Крвките по секундарното отпуштање е обложено со боја на акрилна смола базирана на вода на површината.
- Готови производ: Откако ќе заврши облогата, површината се исуши, а по сушењето, садот е спакуван и складиран.
Време на објавување: март-20-2024 година